Grasping the Different Categories of Nuts and Bolts
As you embark on a construction and do-it-yourself project, the importance of selecting appropriate nuts and bolts cannot be overstated. These fasteners act as a foundation of numerous uses, ensuring structure, integrity, and safety. Given a wide range of options available—all designed for distinct purposes—understanding the basics of nuts and bolts is essential for those who want to address fixes, build items, or embark on major renovations.
In this complete guide, we shall delve into various kinds of nuts and bolts, exploring their applications and applications. Starting with the most common bolts to specific fasteners, we’ll cover all you should understand to help you formulate informed choices and select the right tools for your projects. Whether you're wondering about the differences between machine-type bolts and structural bolts and trying to figure out when to use a flange nut, this is your comprehensive resource for understanding the realm of nuts and bolts.
Categories of Fasteners and Bolts
As it comes to understanding nuts and bolts, it is important to acknowledge the different types available and their specific applications. Fasteners are typically categorized based on their configuration and functionality. Wholesale Bolts and Nuts include hex bolts, which possess a hexagonal head and are ideal for general fastening tasks; carriage fasteners, characterized by a rounded head and a square neck for added grip; and lag fasteners, designed for heavy-duty applications and made with a wide, flat head that allows for greater torque. Each type serves individual purposes and is often selected based on the requirements of the task at hand.
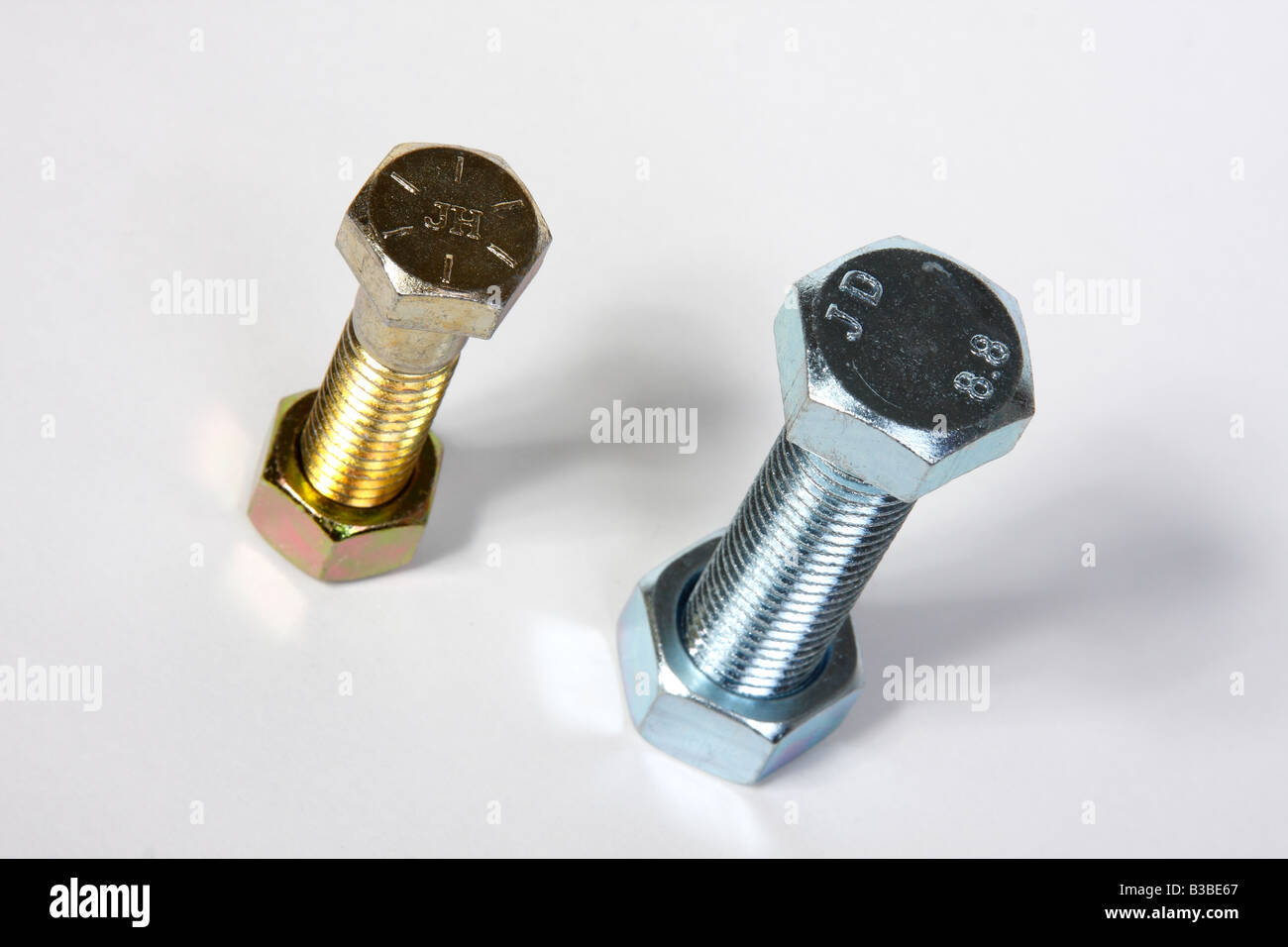
Fasteners, the complements to bolts, also come in multiple shapes and sizes. Regular hex nuts are the most prevalent, allowing for safe fastening when paired with bolts. Locking nuts provide extra safety against loosening, making them suitable for high-vibration applications. Flanged nuts, which have a wider base, spread pressure more evenly and are used where a larger surface area is helpful. Understanding these choices helps in choosing the right nut for multiple fastening situations, ensuring both security and effectiveness.
In addition to standard types, specific nuts and bolts cater to unique demands in specific industries. For instance, titanium fasteners are favored in aerospace applications for their lightweight yet durable nature, while nylon lock nuts prevent loosening due to vibration. Comprehending these variations not only aids in making knowledgeable choices but also enhances the overall strength of constructions or repairs. Selecting the right combination of nuts and bolts is essential in achieving the desired strength and durability for any project.
Selecting the Proper Fastener
Selecting the best fastener is essential for the effectiveness and durability of any project. The choice between bolts and nuts often hinges on the substances being joined and the required robustness. For wood applications, lag bolts are frequently used due to their ability to anchor firmly, while in metalwork, machine bolts with matching fasteners are the preferred choice. Grasping the specific needs of your project, such as load capacity and environmental factors, will guide you in choosing the best choice.
Moreover, the type of threads plays a significant role in fastener selection. Coarse threads are generally better for softer substances, allowing for faster assembly, while tight threads provide greater holding strength in more robust substances. If you are unsure which type to select, it is beneficial to familiarize yourself with the nuances of threading, as well as the standards for metric system and imperial fasteners. An informed decision can prevent potential issues down the road, ensuring better operation and safety.
Lastly, taking into account the finish and substance of the fasteners is essential. Stainless steel bolts offer excellent corrosion resistance, making them appropriate for outdoor projects, while zinc-plated fasteners may serve well in arid environments. Be sure to evaluate the specific environment your fasteners will face, including potential exposure to water or chemicals, to select materials that will withstand the test of time. This attention to precision in selecting the right fastener will ultimately enhance the durability and reliability of your work.
Types of Materials and Finishes
When select fasteners & bolts, the materials used play a significant part in determining their performance & suitability for specific purposes. Frequent materials are iron, copper alloy, and titanium, each delivering distinct advantages. Steel is favored for its robustness & durability, making it ideal for intensive projects. Brass, on the contrary, shows excellent resilience to corrosion and is often used in water systems and electrical applications. Ti is known for its lightweight properties and outstanding strength-to-weight, making it a preferred choice for aerospace and high-tech engineering applications.
Treatments greatly enhance the lifespan and performance of fastening devices. Zinc coatings and galvanization are frequently used methods for safeguarding steel fasteners from rust, with galvanization providing a more robust protective layer. However, the decision of finish is based on the conditions in which the fasteners operate. For example, SS bolts inherently resist corrosion without any additional coating, making them suitable for outdoor and marine uses where exposure to moisture is a factor of importance.
Grasping the materials and coatings that are available helps ensure that you choose the suitable fasteners for your certain project requirements. Regardless of whether you need bolts that can tolerate harsh environments or those that ensure consistent strength, understanding of materials will empower you to make educated decisions that enhance the strength & performance of your assembly.